By Clint Jenkins, Jason Bossier, and Joe Swann
Since 1953, CROM has been using shotcrete to build and restore essential infrastructure. In striving to provide a comprehensive and long-lasting solution for even the most complex structures and systems, our team relies on the strength, durability, creativity and adaptability of shotcrete in wide ranging and complex construction scenarios, making it a compelling choice for our clients.
CASE STUDY #1
SHOTCRETE TUNNEL STABILIZATION (8TH AVENUE RESERVOIR IMPROVEMENT PROJECT)
Metro Water Services in Nashville, TN determined that their historic 51-million-gallon (190-million-liters) reservoir, built in 1889, had reached its useable life. Faced with the decision to either demolish the existing structure and build a new tank in its place or rehabilitate the structure to extend its life, Metro Water Services determined the historic 8th Avenue Reservoir played a crucial role in the community — the tank was not only a landmark fixture in the community but was still needed to supply drinking water to a significant component of the Nashville population. Metro Water Services decided to construct a new tank on the interior of the existing reservoir wall and leave the exterior reservoir wall in place, capturing the historical architectural features.
The design approach required construction of a tunnel through the base of the original reservoir to facilitate access to the interior, for the construction and maintenance of the new wall. CROM was selected as the shotcrete specialty contractor to install the reinforcing steel and apply shotcrete to the tunnel walls and overhead. CROM used both a silica fume enhanced fiber-reinforced mortar as well as
a 5000 psi traditional wet-mix shotcrete. The excavation and rock anchor installations were performed by outside specialty contractors.
After the tunnel was excavated, all exposed surfaces were abrasive blasted then rock anchors and reinforcing steel were installed. During shotcrete placement, thin strips of foam rubber material were used as a guide to ensure proper coverage over the reinforcing steel. Finally, the final shotcrete surface used a soft broom finish.
In the end, CROM placed 1400 bags of shotcrete material and 36 yd³ (28 m³) of 5000 psi shotcrete.
CASE STUDY #2
STEEL SILO LINING PROJECT (MID-WESTERN UNITED STATES)
CROM was asked by Robinson Mechanical Contractors Inc. to be the specialty shotcrete contractor in the shotcrete lining of two existing steel lead ore storage silos. The silos were originally built in 1967 as part of the mill’s lead ore refining process, and after 50 years of use, the original structural steel shell had degraded.
The general contractor’s design team provided CROM with the specifications for an interior liner solution, applying 8 in. (200 mm) of wet-mix shotcrete over the existing steel supporting members and attaching it to the shell using welded Nelson studs and a mat of reinforcing bars tied at 12 in. (300 mm) on center each way. The 5000 psi designed shotcrete mix would be applied in successive layers until the section thickness of 8 in. was achieved with a tolerance of plus or minus 0.5 in. (13 mm) The final application of shotcrete would receive a fine-broom finish.
Working together, CROM, the silo owner, and the general contractor created a plan that would consider and address any obstacles before beginning construction. The owner requested that renovation of the two silos be conducted while their refining process remained in operation. This meant that there would be no interior inspection of the structure prior to construction start. CROM knew some remedial structural repairs would need to take place prior to applying shotcrete to the liner, as a visual inspection showed there were many areas in the silos’ outer shell that were severely corroded from age, use, and environmental degradation.
The general contractor repaired all defects and holes in the original steel silo walls. CROM’s Vehicle Mounted Aerial Platform (VMAP) then provided safe access for shotcreters (formerly called nozzlemen) and finishers. The hopper-floors at the bottom of the silos were leveled off with existing ore to provide a flat base for staging. Using the VMAP, CROM craftsmen attached the reinforcing steel to the Nelson studs welded to the steel shell.
The general contractor’s team designed, cut, and removed a section of the steel silo wall for construction access, allowing CROM to place the VMAPs, staging, and work platform. This also served as access to remove shotcrete rebound and debris associated with the shotcrete placement of the liner. Upon set-up completion, we were able to begin the shotcrete placement of the concrete liner
on the silo walls.
In the end, CROM placed 500 yd³ (380 m³) of 5000 psi shotcrete to restore the two silos for the client.
It is truly paramount to recognize the diversity of solutions available because of the versatility that shotcrete offers. Shotcrete placement provided more efficient, sustainable and durable concrete solutions in these two cases than could have been
achieved with a form-and-pour approach.
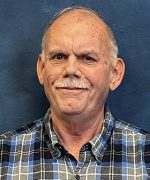
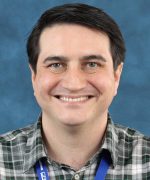
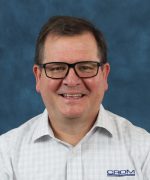